С площадью сварных швов связана несущая способность узла соединения для шести узлов верхнего мостика (табл. 5).
Схема шести узлов соединения подвески с балкой коробчатого сечения показана на рис. 86. На примере узла 9УЕ приведено более подробное описание этих диаграмм. По диаграмме, изображенной слева от подвески, можно определить несущую способность узла соединения. В 95 % случаев при испытании образцов НБС несущая способность узла соединения подвески с коробчатой балкой составляет 72…90 кН. Средняя несущая способность (предел прочности) этого узла 81 кН. Усилия от этих постоянных и временных нагрузок показаны на диаграмме справа от подвески.
Подсчитанная для узла 9УЕ постоянная нагрузка 81 кН, а временная нагрузка в момент обрушения 93 кН. Таким образом, суммарное усилие составило 90 кН.
На рис. 86 показаны аналогичные данные для всех других узлов соединения подвесок с балкой в конструкции верхнего мостика. Эти данные подтверждают, что, за исключением узлов 8УЕ и 10УВ, несущая способность
соединений подвесок с балками равна или лишь немного превосходит величину постоянной нагрузки, передающейся на узел. В то же время во всех случаях сумма постоянных и временных нагрузок превосходит несущую способность (предел прочности) узлов соединений. Таким образом, любой из этих узлов мог не выдержать возможных нагрузок и явиться причиной обрушения переходного мостика.
Разрушение любого соединения мгновенно вызвало бы перераспределение и передачу дополнительных нагрузок на другие узлы. При отсутствии запаса прочности это должно вызвать последовательное разрушение всех остальных узлов соединений, что и произошло на самом деле, когда в результате выхода из строя одного соединения обрушилась вся система переходного мостика.
Фактическое выполнение узла соединения подвесок мостиков 2-го и 4-го этажей отличается от проектного. В проектном решении стержень каждой подвески нераз-резпой, начиная от нижнего мостика до места крепления его к ферме покрытия. Расчетная нагрузка на стержень подвески на уровне нижнего мостика составляла 90 кН. Такая же нагрузка добавлялась от верхнего мостика. Поэтому суммарная нагрузка, воспринимаемая стержнем подвески в его верхней части, вдвое превосходила усилие, действующее в нижней части стержня. В то же время расчетная нагрузка в узлах соединения подвески с коробчатой балкой была одинакова для обоих мостиков и составляла 90 кН.
Фактически каждая подвеска состояла из двух независимых стержней. Верхняя часть подвески от верхнего мостика до потолка выполнена в соответствии с проектом, нижняя часть от верхнего до нижнего мостика оформлена в виде стержня, который смещен на 102 мм внутрь коробчатой балки. При таком решении расчетная нагрузка, переходящая через узлы соединения подвески с коробчатой балкой нижнего мостика, не изменилась, но нагрузка в узлах верхнего мостика удвоилась. Поэтому расчетная нагрузка в узле соединения подвесок с коробчатой балкой верхнего мостика (рис. 87)\’ должна была составить 181 кН.
Следует отметить, что даже без изменения проектного решения несущая способность узла соединения подвески с коробчатой балкой являлась совершенно недостаточной по сравнению с требуемой строительными нормами.
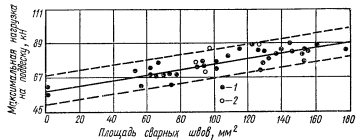
1 — образцы, изготовленные НБС; 2 — образцы, отобранные из конструкций мостиков
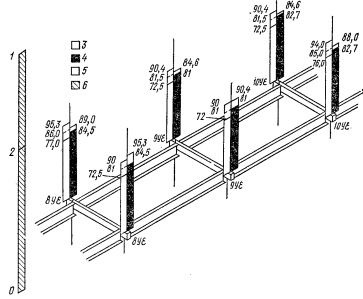
86. Сопоставление несущей способности (предела прочности) узлов соединений коробчатых балок и стержней подвесок мостика 4-го этажа с нагрузками, действующими на узлы в момент разрушения конструкции. Нагрузки и несущая способность (предел прочности) узлов соединений даны в кипах (1 кип =4,5 кН)
1 — расчетная нагрузка 40,7 кН; J—предельная нагрузка 68 кН; 3 — несущая способность узла соединения; 4 —постоянная нагрузка; 5 —временная нагрузка; 6 — расчетные нагрузки в соответствии со строительными нормами Канзас-Сити
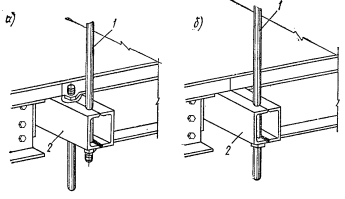
87. Конструкция соединения коробчатой балки со стержнями подвески для мостика 4-го этажа
а — узел, выполненный в натуре; б — конструкция узла, предусмотренная проектом; 1—стержень подвески; 2 — коробчатая балка
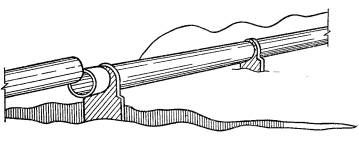
88. Разрушение водовода (воды под напором размыли грунт в основании водовода, в результате чего разрушилась кольцевая опора)

1 — эпюра напряжений от прогиба .трубопровода; 2 — продольные составляющие эпюры напряжении от давления жидкости внутри трубы; 3 — эпюры температурных напряжений; 4 — эпюры дополнительных напряжений вследствие увеличения сечения в стыке и в результате эксцентриситета раструба по ел ношению к основной трубе; 5 — эпюры внутреннего давления в трубе (давление действует нормально но отношению к данному сечению)