Результаты химического анализа показали:
сталь уголков верхнего пояса по содержанию углерода, марганца, серы, фосфора и кремния соответствует марки стали СтЗкп;
сталь уголков нижнего пояса по содержанию углерода (0,23…0,25 %) и серы (0,06%)\’ отвечает требованиям действовавшим в то время ГОСТ 380—50 и ГОСТ 380—57 для стали марки СтЗ кипящей, поставлявшейся для несварных конструкций, и не отвечает требованиям, предъявляемым к стали, поставляемой для сварных конструкций, согласно которым содержание углерода не должно превышать 0,22 % и содержание серы—0,055 %.
сталь уголков верхнего пояса по содержанию углерода, марганца, серы, фосфора и кремния соответствует марки стали СтЗкп;
сталь уголков нижнего пояса по содержанию углерода (0,23…0,25 %) и серы (0,06%)\’ отвечает требованиям действовавшим в то время ГОСТ 380—50 и ГОСТ 380—57 для стали марки СтЗ кипящей, поставлявшейся для несварных конструкций, и не отвечает требованиям, предъявляемым к стали, поставляемой для сварных конструкций, согласно которым содержание углерода не должно превышать 0,22 % и содержание серы—0,055 %.
Результаты химического анализа показали:
сталь уголков верхнего пояса по содержанию углерода, марганца, серы, фосфора и кремния соответствует марки стали СтЗкп;
сталь уголков нижнего пояса по содержанию углерода (0,23…0,25 %) и серы (0,06%)\’ отвечает требованиям действовавшим в то время ГОСТ 380—50 и ГОСТ 380—57 для стали марки СтЗ кипящей, поставлявшейся для несварных конструкций, и не отвечает требованиям, предъявляемым к стали, поставляемой для сварных конструкций, согласно которым содержание углерода не должно превышать 0,22 % и содержание серы—0,055 %.
Контрольный химический анализ стали уголков 200X200X16, примененных в уцелевших фермах (таких же, как в обрушившихся), показал, что содержание углерода в восьми образцах из 13 превышает норму для стали СтЗ и находится в пределах 0,25…0,35 % вместо 0,22 %, а серы —до 0,077 % вместо 0,055 %.
сталь уголков верхнего пояса по содержанию углерода, марганца, серы, фосфора и кремния соответствует марки стали СтЗкп;
сталь уголков нижнего пояса по содержанию углерода (0,23…0,25 %) и серы (0,06%)\’ отвечает требованиям действовавшим в то время ГОСТ 380—50 и ГОСТ 380—57 для стали марки СтЗ кипящей, поставлявшейся для несварных конструкций, и не отвечает требованиям, предъявляемым к стали, поставляемой для сварных конструкций, согласно которым содержание углерода не должно превышать 0,22 % и содержание серы—0,055 %.
Контрольный химический анализ стали уголков 200X200X16, примененных в уцелевших фермах (таких же, как в обрушившихся), показал, что содержание углерода в восьми образцах из 13 превышает норму для стали СтЗ и находится в пределах 0,25…0,35 % вместо 0,22 %, а серы —до 0,077 % вместо 0,055 %.
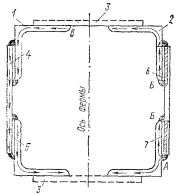
78. Cхема распространения трещин в местах разрыва нижнего поиса 1 — наружная ветвь пояса; 2 — внутренняя ветвь пояса; 3 — решетка; 4—7 — щели соответственно 1,5; 1; 2 и 3 мм
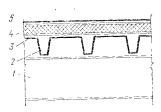
80. Конструкция покрытия
1 — стальной прогон; 2 — стальной профилированный настил; 3 — пароизоляция; 4 — пенополистпрол 50 мм: 5 — водоизоляционный ковер
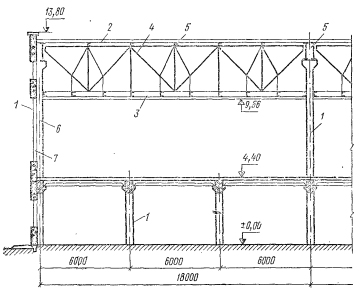
79, Поперечный разрез части корпуса
1 — колонна; 2 — покрытие; 3 — подвесной потолок; 4— стальная стропильная ферма; 5 — подстропильные стальные балки; 6 — керамзитобетонные напел»; 7 — стеклопрофилит
1 — колонна; 2 — покрытие; 3 — подвесной потолок; 4— стальная стропильная ферма; 5 — подстропильные стальные балки; 6 — керамзитобетонные напел»; 7 — стеклопрофилит
Распределение содержания сернистых включений в поперечном сечении разрушившихся уголков верхнего пояса главной фермы вблизи узла № 3 и нижнего пояса вблизи узла N° 4 было определено методом снятия отпечатков по Бауману (рис. 78). Полученные отпечатки свидетельствуют о весьма неравномерном распределении сернистых включений по сечению профилей, характерном для кипящей стали. Наблюдается существенное обогащение серой центральных слоев проката, особенно у обушков уголков. Местами наблюдаются скопления грубых сернистых включений в виде строчек значительной протяженности. Следует отметить, что места ликва-ционного обогащения серой совпадают с участками возникновения хрупкого разрушения поясных уголков (точка А на рис. 78).
Контрольные испытания показали, что поставленные заводом «Азовсталь» уголки, примененные в пролетном строении галереи, не удовлетворяют требованиям ГОСТа по относительному удлинению и химическому составу для стали, применяемой в сварных конструкциях.
По действовавшим в то время нормативным документам (глава СНиП П-В.3-62 «Стальные конструкции. Нормы проектирования» и Указания Госстроя СССР от 28 июля 1961 г.) такого вида конструкции в целях предупреждения хрупкого разрушения должны изготавливаться из стали повышенного качества (сталь марки СтЗ полуспокойная при температуре эксплуатации —30 °С и выше и сталь марки СтЗ спокойная при температуре эксплуатации ниже —30°С). Однако во время проектирования конструкций (1958 г.)\’ эти требования не были регламентированы.
Так как сталь СтЗ кипящая склонна к хрупкому разрушению при низких температурах, для металлических конструкций конвейерных галерей ока не допускается.
Нижний пояс узла № 4 главной фермы, расположенный со стороны примыкания поперечной галереи, разрушился по сварному шву, соединяющему вертикальный лист 6=12 мм с узловой фасонкой со стороны узла № 5. Со стороны внутренней ветви пояса обнаружен значительный непровар в месте стыка вертикали с косынкой на всю длину шва. Глубина непровара колеблется от 5 до 11 мм. В середине шва (по длине) в зазор стыка вложена прямоугольная металлическая вставка длиной 70 мм и толщиной около 10 мм. Стыковой сварной шов наложен поверх вставки, при этом по боковым граням вставки сплавление с металлом шва отсутствует. Ширина стыкового шва на участке вставки достигает 20… …23 мм; формирование шва плохое. Подварочный шов имеется, однако он не перекрывает зазора стыка.
Качество угловых швов, присоединяющих вертикальные листы к перьям уголков, низкое; имеются подрезы до 3 мм и плохое формирование.
Разрушение уголков внутренней ветви пояса хрупкое, внешней ветви — местами пластическое. Разрушение началось с внутренней ветви пояса. Образование трещин началось около мест острой концентрации напряжений в местах сопряжения стыкового шва с окончанием связующего шва, прикрепляющего вертикаль к уголку у обушка (точка А на рис. 78), и в местах пересечения угловых швов, наложенных по перьям уголков, со стыковым швом (точка Б). Дальнейшее развитие трещин протекало, как указано на рис. 78. Первые трещины образовались в верхнем уголке около обушка. После разрыва внутренней ветви внешняя ветвь должна была воспринять удвоенное усилие с изгибом вследствие эксцентричного его приложения. Разрыв этой ветви начался с пера верхнего уголка в месте концентрации напряжений (точка В на рис. 78). Последовательность трещин показана стрелками на той же схеме,
При полном проваре стыка напряжение в поясе составляет 143 МПа, а в месте концентрации напряжений при минимальном значении коэффициента концентрации для рассматриваемого случая, равного 4, напряжение в точке А составляет 143-4 = 572 МПа, т. е. больше временного сопротивления, установленного контрольным испытанием, — 391…430 МПа.
При предположении, что вертикал полностью выключился из работы вследствие непровара стыка, номинальное напряжение в этом месте (точка Л) составит 214 МПа, т. е. находится на уровне допускаемых 210 МПа, но из-за наличия концентрации поднимается до 856 МПа.
После разрыва внутренней ветви пояса условное краевое напряжение без учета развития пластических деформаций в наружной ветви и даже без учета концентрации составляет 3710 МПа, что почти в 7 раз превышает установленное испытаниями временное сопротивление.
Как видно, напряжение в точке А вследствие концентрации дошло до значения, превышающего временное сопротивление. При пластичном материале это напряжение не вызывает появления трещин, так как сталь в местах высоких напряжений течет и вследствие этого пиковые напряжения снижаются до величины предела текучести. При металле, обладающем пониженными пластическими свойствами или утратившем их, повышенные напряжения в местах концентрации приводят к хрупкому разрушению.
Кипящая сталь марки СтЗ имеет порог хладноломкости при температуре 0…25 °С, поэтому в день аварии (температура —36,5 °С) она пластические свойства утратила.
Контрольные испытания показали, что поставленные заводом «Азовсталь» уголки, примененные в пролетном строении галереи, не удовлетворяют требованиям ГОСТа по относительному удлинению и химическому составу для стали, применяемой в сварных конструкциях.
По действовавшим в то время нормативным документам (глава СНиП П-В.3-62 «Стальные конструкции. Нормы проектирования» и Указания Госстроя СССР от 28 июля 1961 г.) такого вида конструкции в целях предупреждения хрупкого разрушения должны изготавливаться из стали повышенного качества (сталь марки СтЗ полуспокойная при температуре эксплуатации —30 °С и выше и сталь марки СтЗ спокойная при температуре эксплуатации ниже —30°С). Однако во время проектирования конструкций (1958 г.)\’ эти требования не были регламентированы.
Так как сталь СтЗ кипящая склонна к хрупкому разрушению при низких температурах, для металлических конструкций конвейерных галерей ока не допускается.
Нижний пояс узла № 4 главной фермы, расположенный со стороны примыкания поперечной галереи, разрушился по сварному шву, соединяющему вертикальный лист 6=12 мм с узловой фасонкой со стороны узла № 5. Со стороны внутренней ветви пояса обнаружен значительный непровар в месте стыка вертикали с косынкой на всю длину шва. Глубина непровара колеблется от 5 до 11 мм. В середине шва (по длине) в зазор стыка вложена прямоугольная металлическая вставка длиной 70 мм и толщиной около 10 мм. Стыковой сварной шов наложен поверх вставки, при этом по боковым граням вставки сплавление с металлом шва отсутствует. Ширина стыкового шва на участке вставки достигает 20… …23 мм; формирование шва плохое. Подварочный шов имеется, однако он не перекрывает зазора стыка.
Качество угловых швов, присоединяющих вертикальные листы к перьям уголков, низкое; имеются подрезы до 3 мм и плохое формирование.
Разрушение уголков внутренней ветви пояса хрупкое, внешней ветви — местами пластическое. Разрушение началось с внутренней ветви пояса. Образование трещин началось около мест острой концентрации напряжений в местах сопряжения стыкового шва с окончанием связующего шва, прикрепляющего вертикаль к уголку у обушка (точка А на рис. 78), и в местах пересечения угловых швов, наложенных по перьям уголков, со стыковым швом (точка Б). Дальнейшее развитие трещин протекало, как указано на рис. 78. Первые трещины образовались в верхнем уголке около обушка. После разрыва внутренней ветви внешняя ветвь должна была воспринять удвоенное усилие с изгибом вследствие эксцентричного его приложения. Разрыв этой ветви начался с пера верхнего уголка в месте концентрации напряжений (точка В на рис. 78). Последовательность трещин показана стрелками на той же схеме,
При полном проваре стыка напряжение в поясе составляет 143 МПа, а в месте концентрации напряжений при минимальном значении коэффициента концентрации для рассматриваемого случая, равного 4, напряжение в точке А составляет 143-4 = 572 МПа, т. е. больше временного сопротивления, установленного контрольным испытанием, — 391…430 МПа.
При предположении, что вертикал полностью выключился из работы вследствие непровара стыка, номинальное напряжение в этом месте (точка Л) составит 214 МПа, т. е. находится на уровне допускаемых 210 МПа, но из-за наличия концентрации поднимается до 856 МПа.
После разрыва внутренней ветви пояса условное краевое напряжение без учета развития пластических деформаций в наружной ветви и даже без учета концентрации составляет 3710 МПа, что почти в 7 раз превышает установленное испытаниями временное сопротивление.
Как видно, напряжение в точке А вследствие концентрации дошло до значения, превышающего временное сопротивление. При пластичном материале это напряжение не вызывает появления трещин, так как сталь в местах высоких напряжений течет и вследствие этого пиковые напряжения снижаются до величины предела текучести. При металле, обладающем пониженными пластическими свойствами или утратившем их, повышенные напряжения в местах концентрации приводят к хрупкому разрушению.
Кипящая сталь марки СтЗ имеет порог хладноломкости при температуре 0…25 °С, поэтому в день аварии (температура —36,5 °С) она пластические свойства утратила.